Grinding Wheels
Enhancing Precision and Efficiency
Grinding wheels play a pivotal role in various industries, serving as indispensable tools for material removal and shaping. Composed of abrasive particles bonded together, these wheels are engineered to withstand high temperatures and mechanical stresses encountered during grinding processes. Their versatility extends across metals, ceramics, and other materials, contributing to applications ranging from manufacturing to construction. In the realm of metalworking, grinding wheels ensure precise shaping of components, while in construction, they facilitate the smoothing of surfaces.
As technology advances, the development of innovative grinding wheel compositions and structures continues to refine their performance, enhancing precision and efficiency in material processing
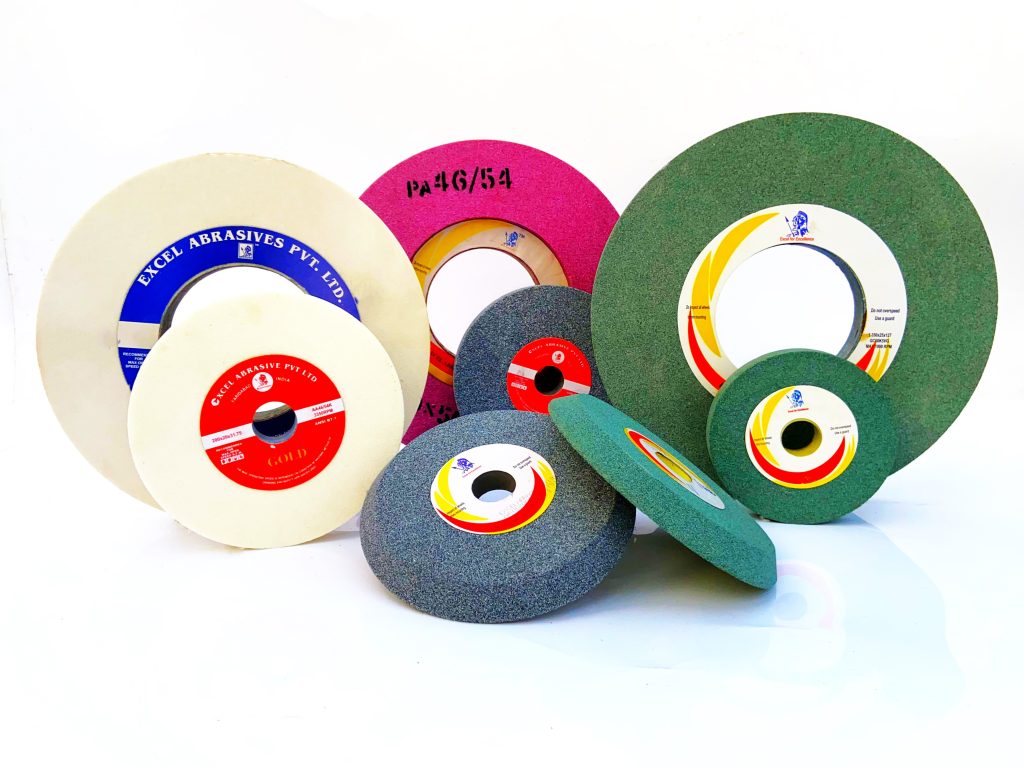
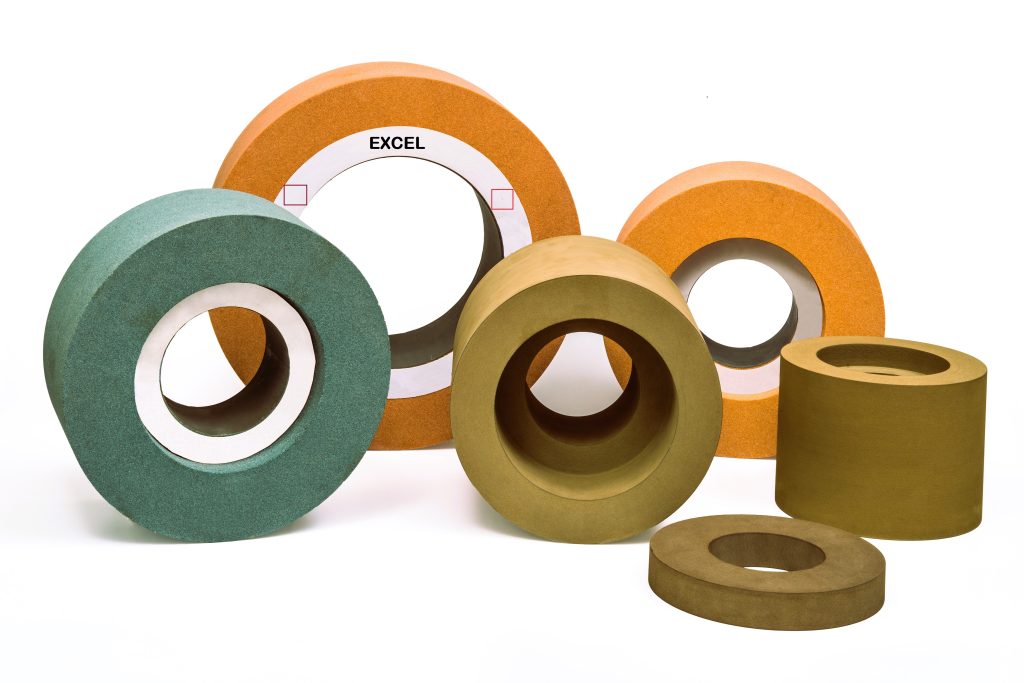
Rubber Control & Centreless Wheels
EXCEL Abrasives manufacturer to produce Rubber Bonded Control wheels
The Rubber bonded Control and Centreless grinding wheels for
- Bearing Industry
- Automobile Industry
- Hydraulic Industry
- Cutting Tool Industry
- General Purpose
RUBBER CONTROL WHEEL Product Features:
- Longer wheel-life
- Lesser dressing frequency
- Superior form retention
- Superior surface finish
Application | Product Recommendation |
---|---|
For All Conventional Centreless Grinding | A80 R R |
For Fine & Precision Grinding | A120 RR |
For Fine & Precision Grinding | A150 RR |
Abrasive | Grit Size | Hardness | Bond Type | Dia (mm) | Thickness (mm) |
---|---|---|---|---|---|
Brown Aloxide (A) | 80 - 180 | R -T | Rubber (R) | 100 - 508 | 100 - 350 |
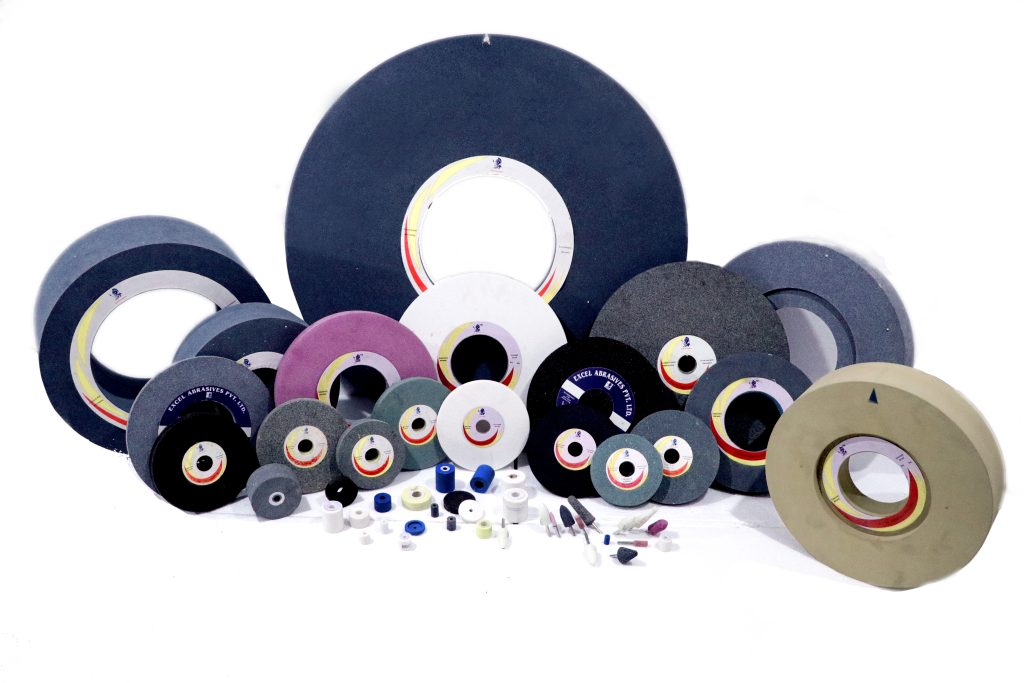
Tailoring Solutions for Diverse Applications
Grinding wheels come in a myriad of types, each tailored to specific applications and materials. Abrasive wheels, such as aluminum oxide and silicon carbide variants, find extensive use in general-purpose grinding, while diamond and cubic boron nitride (CBN) wheels are preferred for harder materials like carbides and ceramics. The bonding matrix, be it vitrified, resin, or metal, further customizes the wheel’s characteristics, influencing factors such as cutting efficiency and heat resistance. For precision grinding tasks, like those in the aerospace or medical industries, specialized wheels with intricate profiles and high tolerances are employed.
Understanding the diverse types of grinding wheels available allows industries to select the most suitable tool for their specific needs, ensuring optimal results in various material processing applications.
Centreless Grinding
- EXCEL range of Centreless Grinding Wheels include the versatile and time tested bond systems V10, V45, V2016, V1092, VG which provides high performance and is available in different sizes and grit combinations. These wheels are ideal for difficult – to – grind materials, which gives safety tolerances upto 60 mps. The unique characteristics of the highly fusible and cool cutting bonds used also imparts:
- Excellent form retention
- Excellent component finish
- Lesser dressing frequency
- EXCEL Abrasives” is the newly developed bond system which imparts excellent with superior form retention and improved wheel life.
User Industries:
- Bearing Industry
- Cutting Tool Industry
- Automobile Industry
- Bar Grinding Industry
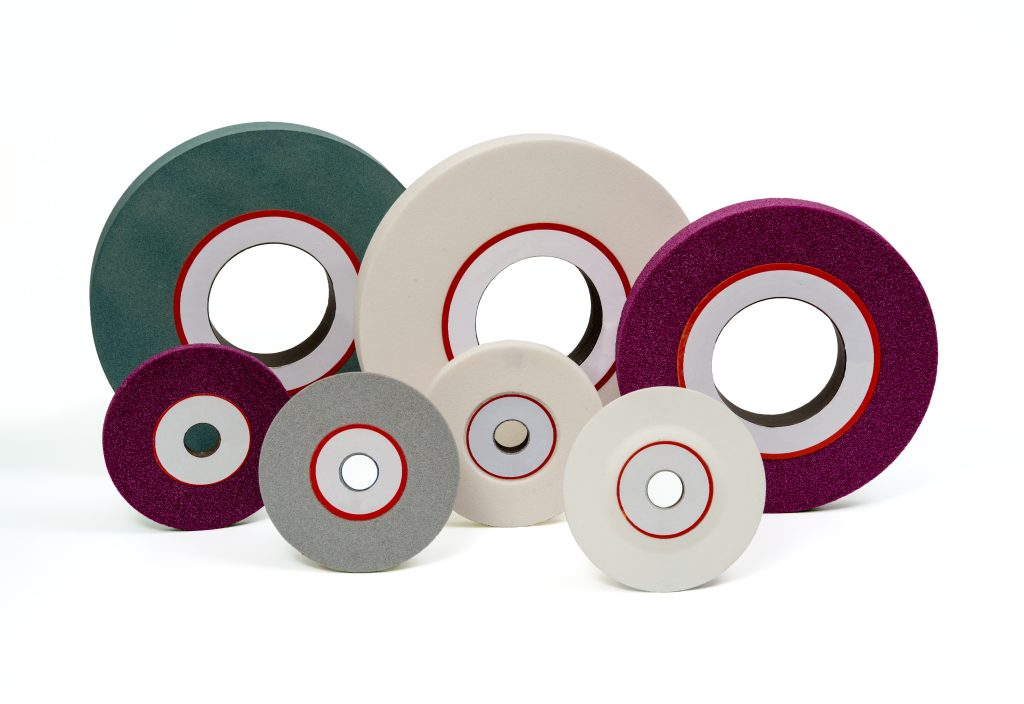
ROUGHING – CENTRELESS GRINDING
Product Features
- Higher Stock Removal
- Special Bond* EXCEL Abrasives” for excellent performance
Specification | Dia (mm) | Thickness (mm) | Product Type | |
---|---|---|---|---|
Value for money | A463 K5 V1035 | 350-750 | 75-250 | Type 1,5 & 7 |
Value for money | A463 L5 V1035 | 350-750 | 75-250 | Type 1,5 & 7 |
Value for money | A463 M5 V1035 | 350-750 | 75-250 | Type 1, 5 & 7 |
Value for money | A463 N5 V1035 | 350-750 | 75-250 | Type 1, 5 & 7 |
Value added product | A463 K5 V2016 | 350-750 | 75-250 | Type 1,5 & 7 |
Value added product | A463 L5 V2016 | 350-750 | 75-250 | Type 1,5 & 7 |
Value added product | A463 M5 V1035 | 350-750 | 75-250 | Type 1, 5 & 7 |
Value added product | A463 N5 V1035 | 350-750 | 75-250 | Type 1,5 & 7 |
Premium Product | A463 K5 V10X3 | 350-750 | 75-250 | Type 1,5 & 7 |
Premium Product | A463 L5 V10X3 | 350-750 | 75-250 | Type 1,5 & 7 |
Premium Product | A463 M5 V10X3 | 350-750 | 75-250 | Type 1, 5 & 7 |
Premium Product | A463 N5 V10X3 | 350-750 | 75-250 | Type 1,5 & 7 |
Wheel Types

FINISHING – CENTRELESS GRINDING
Product Features
- Better Surface finish
- Special Bond” EXCEL Abrasives” for excellent performance
- Higher Productivity / Efficiency
Specification | Dia (mm) | Thickness (mm) | Product Type | |
---|---|---|---|---|
Value for money | A60 K5 V1035 | 350-750 | 75-250 | Type 1, 5 & 7 |
Value for money | A60 L5 V1035 | 350-750 | 75-250 | Type 1, 5 & 7 |
Value for money | A60 M5 V1035 | 350-750 | 75-250 | Type 1, 5 & 7 |
Value for money | A60 N5 V1035 | 350-750 | 75-250 | Type 1, 5 & 7 |
Value added product | A60 K5 V2016 | 350-750 | 75-250 | Type 1, 5 & 7 |
Value added product | A60 L5 V2016 | 350-750 | 75-250 | Type 1, 5 & 7 |
Value added product | A60 M5 V2016 | 350-750 | 75-250 | Type 1, 5 & 7 |
Value added product | A60 N5 V2016 | 350-750 | 75-250 | Type 1, 5 & 7 |
Premium Product | A60 K5 V10X3 | 350-750 | 75-250 | Type 1, 5 & 7 |
Premium Product | A60 L5 V10X3 | 350-750 | 75-250 | Type 1, 5 & 7 |
Premium Product | A60 M5 V10X3 | 350-750 | 75-250 | Type 1, 5 & 7 |
Premium Product | A60 N5 V10X3 | 350-750 | 75-250 | Type 1,5 & 7 |
Wheel Types
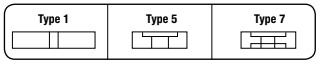
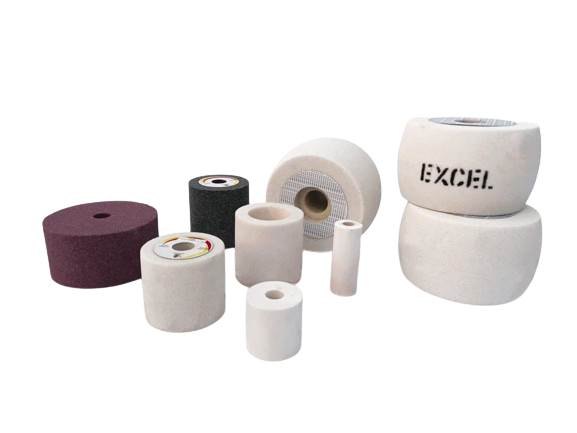
Internal Grinding Wheels
Product Description
Internal grinding is a process of finishing the inside diameter of the component to an accurate size and desired finish. The high contact areas in this application poses a challenge and EXCEL offers both conventional & high performance wheels.
Product Features
- Better form retention
- Excellent component finish
- Less dressing frequency
Material | Specification | Dia (mm) | Thickness (mm) |
---|---|---|---|
Value Added Product | SA601 TDV144 | 10-120 | 5-75 |
Value Added Product | 55A601 J7 VC500 | 10-120 | 5-75 |
Value Added Product | AA60 K5 V8 | 10-120 | 5-75 |
Premium Product | 3MSB601 J6 V500 | 10-120 | 5-75 |
Premium Product | 71HA601 17 VC500 | 10-120 | 5-75 |
Advancements in Grinding Wheel Technology
Modern manufacturing demands have propelled the evolution of grinding wheel technology. Advanced materials, coatings, and manufacturing processes have led to the creation of grinding wheels that offer enhanced durability, reduced heat generation, and improved material removal rates. Nanotechnology is making its mark, introducing nanostructured abrasives that provide superior performance in terms of precision and surface finish. Furthermore, the incorporation of smart technologies, such as sensors embedded in grinding wheels, enables real-time monitoring and adjustment of grinding processes.
As industries continue to face new challenges, the ongoing innovation in grinding wheel technology ensures that these essential tools evolve to meet the demands of precision engineering and manufacturing in the 21st century.
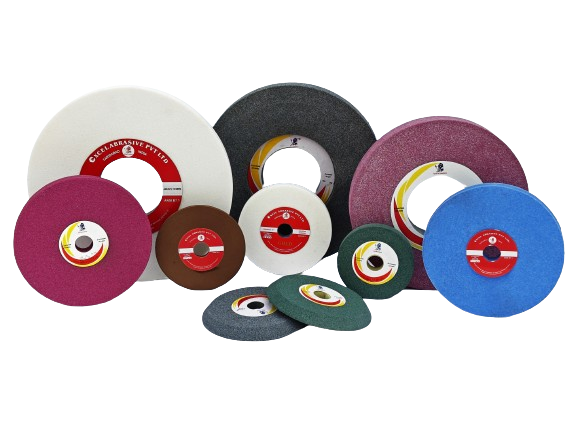